Recap of the Challenge
In our last blog, we looked at energy efficiency using a concept widely used in commercial construction: Total Cost of Ownership (TCO). We then reviewed a few approaches to building efficient spaces but ran up against three core challenges in the construction and building product spheres. Super-insulated homes often have complex assemblies that are difficult for builders to consistently achieve, many insulations have negative health and environmental consequences, and timelines for planning and building an energy-efficient home are often too long.
Simplicity & Accuracy
One of the enduring benefits of travel is that you get to see how different communities and people deal with the same problems as you but end up with different and, occasionally, better solutions. In May, I had the privilege to visit Germany to see how builders use local wood resources to construct homes that achieve passive house standards. The mind-expanding aspect of their approach is its simplicity – boards nailed together to form a solid wall of 5-15 layers, each layer running crossways to its neighbours.
Like me, you’re possibly wondering how this can be a high-performance wall. We’ll address that shortly. But first, let’s look at how these “big wood walls” are made.
I visited a production facility owned by a carpentry company that specializes in multi-family residential construction. Kiln-dried boards in random widths are purchased from nearby sawmills. The boards are planed to the exact thickness and receive a grooved pattern on one face.
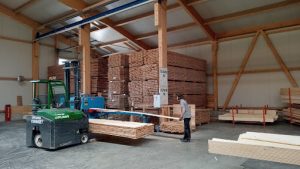

The grooves help to reduce sound transmission and improve the insulative quality of the wall. Boards are fed into a CNC assembler that places and nails each board in place, creating a wall billet of up to 4.8m x 6.1m (16’ x 20’).
This CNC unit places and nails boards to suit the wall’s role in the overall structure.
Once nailing is complete the billets are moved to a CNC cutter that translates an architect’s 3D model into a series of machining steps that create window and door openings, gable cuts, electrical and mechanical chases, and a variety of panel-to-panel connection details. A cutting accuracy of +/- 1mm ensures that panels go together precisely on site, providing air tightness and excellent structural rigidity.
Gantry-type CNC begins to work on a wall billet.
Wall units are labelled, receive a rain cap, and lift straps, and are loaded onto flatbed trucks in an upright position.

In Germany, the use of site cranes is the norm, and every established builder has at least one. The lead carpenter operates the crane via a wireless control set that allows them to always be in the best location to safely lift the panels from the truck, swing them and set them into place. A crew of 4-5 carpenters will install the walls, floors, and roof of a 170 m2 (1800 sq. ft.) home in just three or four days.

The speed and simplicity of the work are astonishing, especially for anyone familiar with typical site-built processes and timelines in Canada. And it’s quiet, with minimal use of saws or other power tools.
Speed of construction is supported by three conditions inherent to the Big Wood Wall: 1) precisely dimensioned and detailed panels, 2) zero site modification, and 3) designs modelled in 3D which include optimized shipping and assembly sequences.
Insulation
So how does a wood wall reach Net Zero or even Passive House levels?
Wood, especially pine, spruce, and other softwood, is intrinsically a “warm” material with a cell structure that is slow to transmit heat or cold. The grooves further slow conductive transfer, by reducing the contact surface area board to board. The whole assembly is solid, dramatically reducing air infiltration even before any wind barrier layer is added.

The walls provide backing for externally applied, uninterrupted insulation. A typical exterior wall of 13 layers and 140mm (5.5”) of wood fibre insulation will approach R50. For extremely cold climates the insulation layer can be increased up to 240mm (9.5”).
A solid wood wall has significant thermal mass, which means that changes in temperature on one surface takes a long time to be telegraphed through to the opposite surface. The number of hours for a change in outdoor temp to be noticed at the interior is called “phase shift” and for most conventionally framed homes will be in the order of 5-7 hours. For the wall in the photo above, its phase shift is 22 hours. Longer phase shifts mean a more comfortable interior with proportionately smaller variations in temperature.
Health & Air Quality
In Germany, and the EU in general, there’s a heightened perception that chemical exposures are connected to negative health consequences. Poor indoor air quality and the incidence of asthma, especially in children, have been linked to chemicals like formaldehyde that off-gas from a variety of manufactured sheet goods and insulations. Consequently, builders and home buyers in Germany have created a strong market for natural and chemical-free building materials.
The Big Wood Wall fits well into the trend toward natural materials, using untreated wood that is nailed together, with no need for chemical-based adhesives. Additionally, wood is hygroscopic which means that it can easily absorb and release moisture, allowing it to act as a humidity regulator. This attribute is particularly beneficial in climates with humid summers and dry winters.
Wood is increasingly understood as being biophilic, a term describing materials and objects that support human feelings of well-being and that confer physical and mental health benefits. It’s why we gravitate toward urban parks and why researchers see a measurable drop in blood pressure and anxiety as people are exposed to flowers, trees, and natural materials where they live and work.
Affordability and the Long View
Early financial analysis suggests that a big wood wall, compared to its closest analog, a CLT wall panel, will be approximately 30% more cost-effective. But, as we’ve previously discussed, a purchase price can never stand in isolation from a host of other life cycle costs like energy use, serviceability, and maintenance. Occupant health and environmental impacts should be valued, though rarely are, at least in the North American context.
In Germany, the Big Wood Wall is widely used in multi-family construction, of up to five storeys in height. Many of these projects, like the apartments shown below, are entering the market as affordable rental units. In some European jurisdictions, homebuyers and developers also receive added financial incentives if their project achieves a high level of energy efficiency. All barriers to building well and attaining the lowest “total cost of ownership” have been removed by these innovative and farsighted authorities.
Mikado Apartments in Baden-Württemberg: achieving net zero takes the sting out of monthly bills.
If you are intrigued by the idea of the Big Wood Wall, I would be delighted to hear from you. Introducing this concept to North America will require a significant pioneering effort. In Europe, the Big Wood Wall has been gaining popularity since 2011, and as per the latest reports, over thirty plants are producing these panels, and more than 7,000 projects have been completed.
Next month we will look at noise transmission in buildings. And yes, that was another significant “light bulb” moment in my travels. People’s perception of noise and their response to it appears to be different from place to place. Join me for a fascinating look at the scientific, historical, and societal aspects of noise in the places where we live.