“Must See” Timber Connections
Two joinery details that change how modern timber frames are made.
Whenever two pieces of timber meet in timber framing, they need to be connected. Carpenters call this connection ‘joinery,’ which involves cutting specific details into two pieces to keep them together. These joinery details are usually hidden from view once the timber frame is assembled.
In this article, we will discuss two joinery details that have made a significant contribution to the visual and strength values of modern timber frames. These details are part of a ‘quiet revolution’ in timber framing, which has been made possible by technology.
Dovetails – the old dovetail connection has been around for centuries. It’s a V-shaped tenon on the end of a timber that slots vertically into a matching pocket in another timber. It’s often used in floor joists, connecting them to larger floor beams. They can also be used for purlins, corbels and wherever a small timber intersects a larger one.
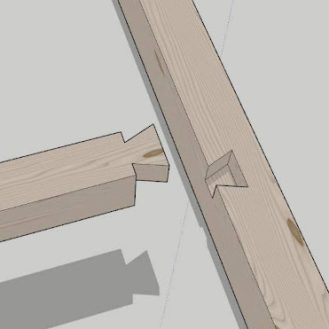
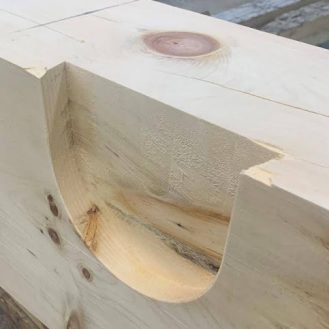
Tapered dovetail mortise in receiving beam
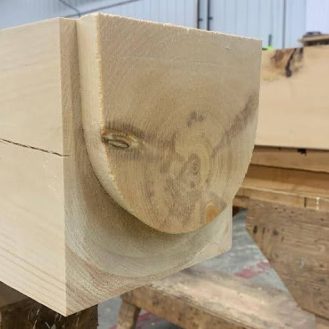
Improved tenon with double taper.
The new type of dovetail features a double taper that pulls timbers together as it settles into place. The new shape provides more contact surface and ensures that the joined pieces stay tight as they adjust to indoor humidity levels. Strength and beauty are given a helping hand, thanks to this smart dovetail design.
Housed Mortise – this is a joinery detail that “fortifies” the typical mortise and tenon connection. Essentially, it’s a step or recess that borders the mortise on all sides, allowing the tenon and the whole connecting timber to be set into the receiving beam or column. In the pre-modern period, a housing was a considerable amount of additional work for a carpenter to create and was therefore used sparingly. Where a timber needed to resist larger rotational or lateral forces (think old mills and larger civic or church buildings) a housed mortise was an effective and worthwhile detail.
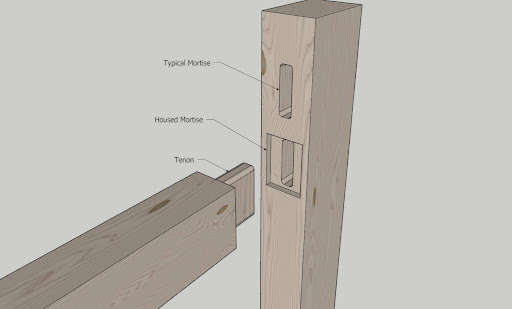
The Housed Mortise allows the incoming timber to be set fully into the receiving column.
With the advent of CNC timber cutting, the effort and time needed to create a housed mortise has been significantly reduced. And while most timber frame projects don’t need the structural benefits of a housed joint, these connections have one additional trait: they’re aesthetically pleasing. The gap that typically can be seen where two timbers meet, disappears, as it happens out of sight, thanks to the recessed housing.
If you’re thinking of a timber frame for your next project, be in touch! You can reach us by phone: 204.377.5000 or by email: info@cstf.ca.