June is a month to honour the vitality, success, and beauty of First Nations, Inuit, and Métis cultures and communities across Canada.
Cornerstone Timberframes joins with our Indigenous neighbours as they celebrate families, communities, lands and cultures. Good things are happening! Canada’s Indigenous Peoples are leading the way forward in stewardship, community building, art, business and governance. When Indigenous Peoples thrive, we all share a better and brighter future.
In recent years, Cornerstone has been privileged to work with many Indigenous communities and partners. Our hearts are full of appreciation for the teachers who have guided us as we learn more about Indigenous cultures and values. In turn, we share a love of wood that shelters and inspires with people who have known the power of wood since time began. It’s led to beautiful collaborations.
From building Powwow circles to healing shelters, cultural spaces, family and youth centres, council chambers, and schools, we witness people who are proudly strengthening their communities, setting their youth on a good path and honouring their elders.
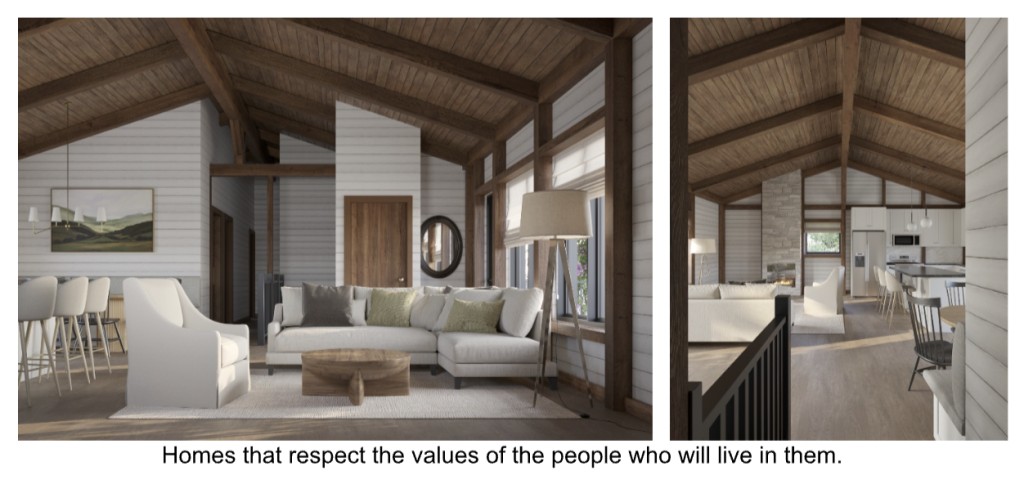
But of all our shared work, we are deeply moved when we see the strength that high-quality homes bring to Indigenous families and communities.
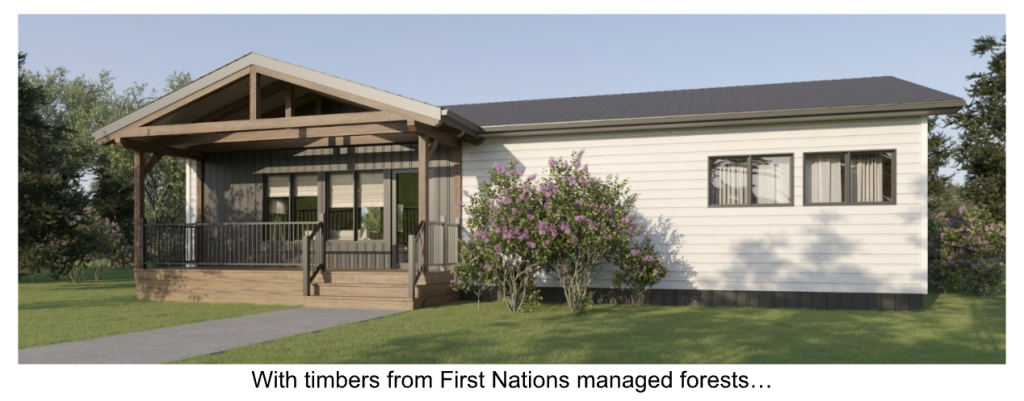
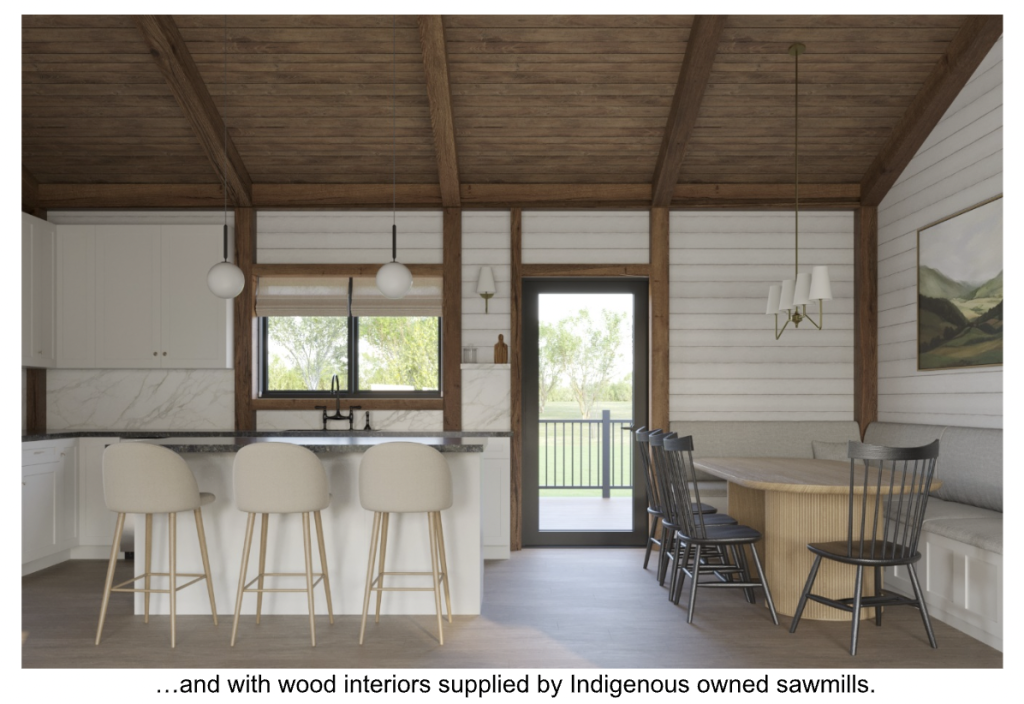
An insight of Indigenous teaching is that everything is connected. When we live in kindness, care and respect, a cycle of goodness is created. When a good home is built, lives are changed for the better.
On June 21st we’ll be celebrating, thankful for our connections to Indigenous communities and friends!