Cornerstone’s Mass Timber Team recently travelled to Denver, Colorado to attend the Mass Timber Group Summit, a conference bringing together the industry’s leading experts, designers and builders.
Day 3 of the Summit was a chance to get out of the conference venue in downtown Denver and visit two project sites where mass timber is being used. For Michael Pankratz, Cornerstone’s vice president and design lead, it was his favourite day. Following university, he spent two formative years working in construction, so any chance to put on a hard hat and see the practical working out of a design is a good time.
Colorado School of Mines “Park Village” in Golden, CO.
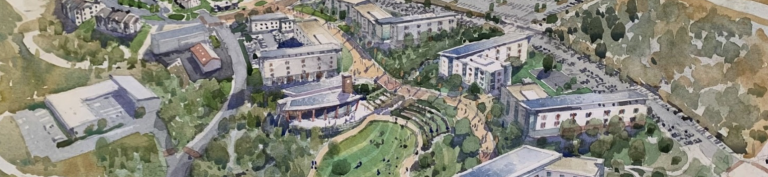
The Mines Park Village is a large site intended to provide a cohesive community for students and their families attending the Colorado School of Mines. Five multi-storey apartments are under construction, arranged around a central community green space. When complete they will provide accommodations for over 1000 residents.
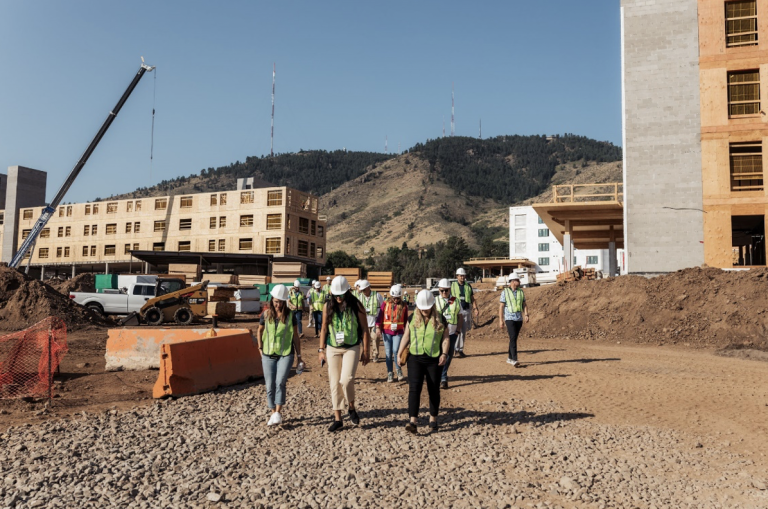
The sunny site will make good use of solar panels to reduce grid power use.
The short project timeline, just 20 months from breaking ground last November, made collaboration between the site developer, architect, and builder essential. The construction approach is hybrid: stick-framed load-bearing walls, cross-laminated timber (CLT) floors, and non-bearing demising walls between units.
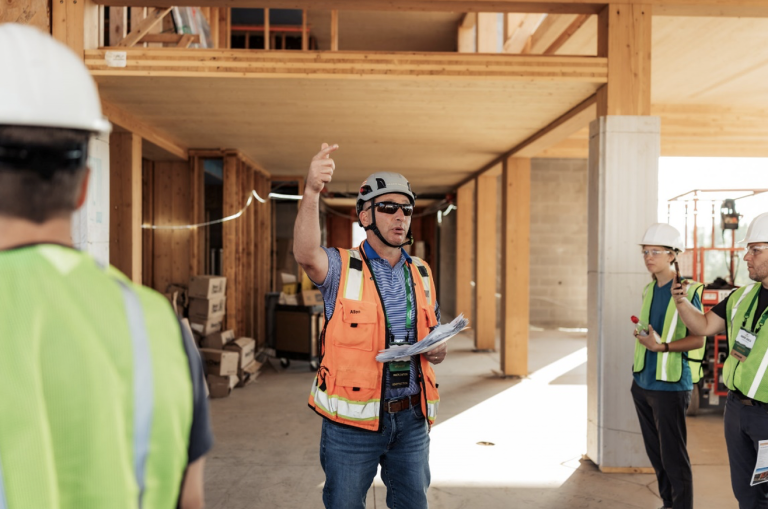
Allen Becker, VP & Field Operations for Milender White describes the construction sequence.
The contractor, Milender-White, has taken three measures to ensure that they stay on schedule:
- Determine every detail ahead of breaking ground. They created a detailed model for each structure, “a digital twin”, that shows every component from fasteners to individual sheets of drywall in each of the five buildings.
- Wall sections are being prefabricated off-site, with backing points and mechanical openings cut and wiring runs installed. Each wall element is numbered to line up with locations identified in the digital twin, and every site worker has a tablet, allowing them to access and quickly identify these locations.
- Self-performance. Rather than subcontracting work to independent trades, Milender-White utilizes its own trade teams to do the work. Everyone is on the same page and committed to their GC’s timelines.
As they toured, Michael noticed the CLT install team, just two workers, making rapid progress on one of the apartment floors. In 20 minutes, they placed five-floor panels, or roughly 1,000 sq. ft. – an amount that a regular framing crew of four would only hope to achieve in a full day’s work. It was a great demonstration of the speed and ease of using mass timber!
When done, the architect anticipates these five apartments will receive LEEDTM Gold certification.
One Line Studio, Greenwood Village, CO
The second tour destination was a recently completed architecture office in Greenwood Village, a tony suburban neighbourhood in Denver’s southeast.
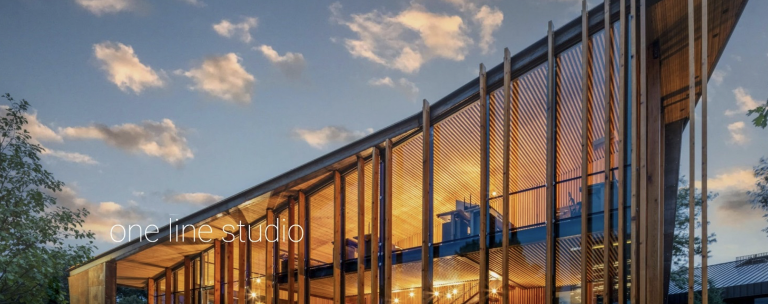
Tim Politis is the Principal Architect for One Line Studio. He felt that when it came time to build their firm’s new studio space, they needed to heed the same advice they give their clients: be bold, try new things and embrace the best sustainable practices.
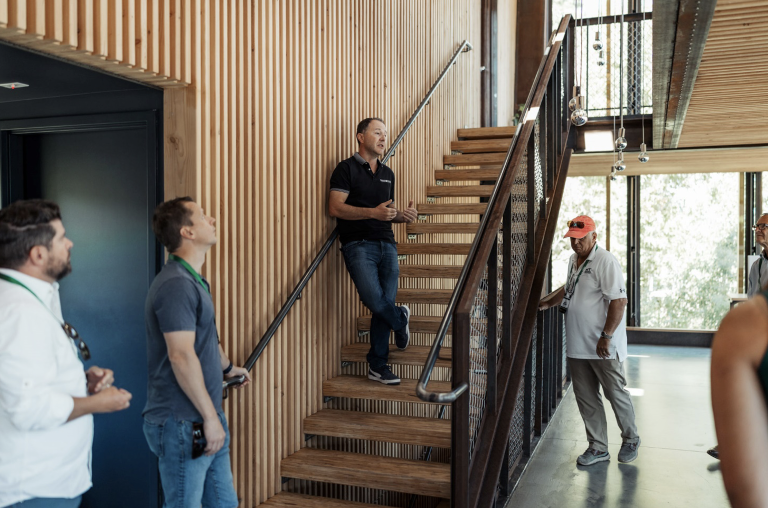
The structure is constructed with mass timber panels called Dowel Laminated Timber (DLT’s). As the name suggests, the 2×6 and 2×8 alternating boards in these panels are held together by hardwood dowels instead of glue or nails. This project is the first to use this form of mass timber in the Denver area. The board-to-board offsets, or baffles are visually pleasing and provide three additional benefits:
- The baffles, allow the open office space to be surprisingly quiet, greatly reducing sound bounce.
- Electrical conduit, and mechanical ventilation openings can be neatly concealed within the baffles, creating a more uninterrupted, uniform look.
- The baffles effectively reduce glare from the building’s large window walls, an important consideration for designers whose eyes are glued to computer screens!
An intentional design choice was to leave the wood untreated—no finishes were applied. This decision was also extended to the building’s structural and decorative steel elements and to the natural plantings around the studio. This approach has already garnered a few pointed comments in a neighborhood of expensive homes and neatly trimmed yards. But like other innovators, Tim Politis is unfazed; he’s committed to seeing his vision and studio lead the way to more sustainable construction.
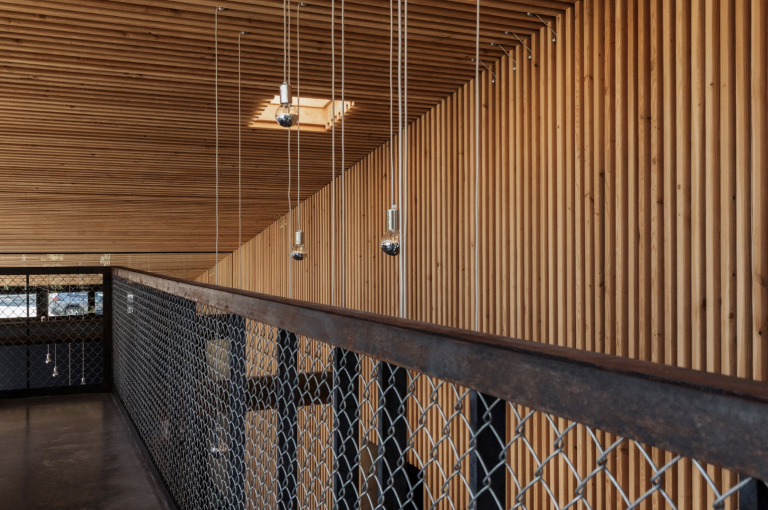